AUS/NZ RESPIRATORY PROTECTION STANDARDS - AS/NZS 1716:2012, AS/NZS 1715:2009
- Rebekah McCutcheon
- Apr 3
- 8 min read
Updated: Apr 6
AS/NZS 1716:2012, AS/NZS 1715:2009 - The AUS Respirator Protection Standards and What They Mean To You
Why Respiratory Protection Matters
Every year, thousands of workers across Australia and New Zealand suffer from respiratory illnesses caused by exposure to hazardous airborne contaminants. According to Safe Work Australia, occupational lung diseases—such as silicosis, asbestosis, and occupational asthma—remain a significant workplace safety concern, with inadequate respiratory protection being a leading cause. Australia and New Zealand have established strict respiratory protection standards including AS/NZS 1716:2012 and AS/NZS 1715:2009 to regulate business compliance and keep workers safe.
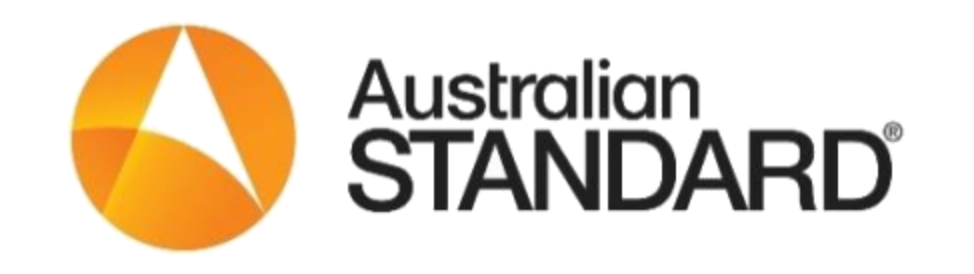
For industries like construction, mining, manufacturing, and healthcare, ensuring workers have the right respiratory protective equipment (RPE) is not just about compliance—it’s about safeguarding long-term health. Without proper protection, exposure to harmful dust, gases, and airborne pathogens can lead to severe and irreversible health conditions.
To mitigate these risks, Australia and New Zealand established respiratory protection standards that dictate how businesses select, use, and maintain respiratory protective devices (RPD) to ensure they provide effective protection. Understanding these regulations is essential for businesses to maintain compliance, avoid penalties, and, most importantly, protect their workers.
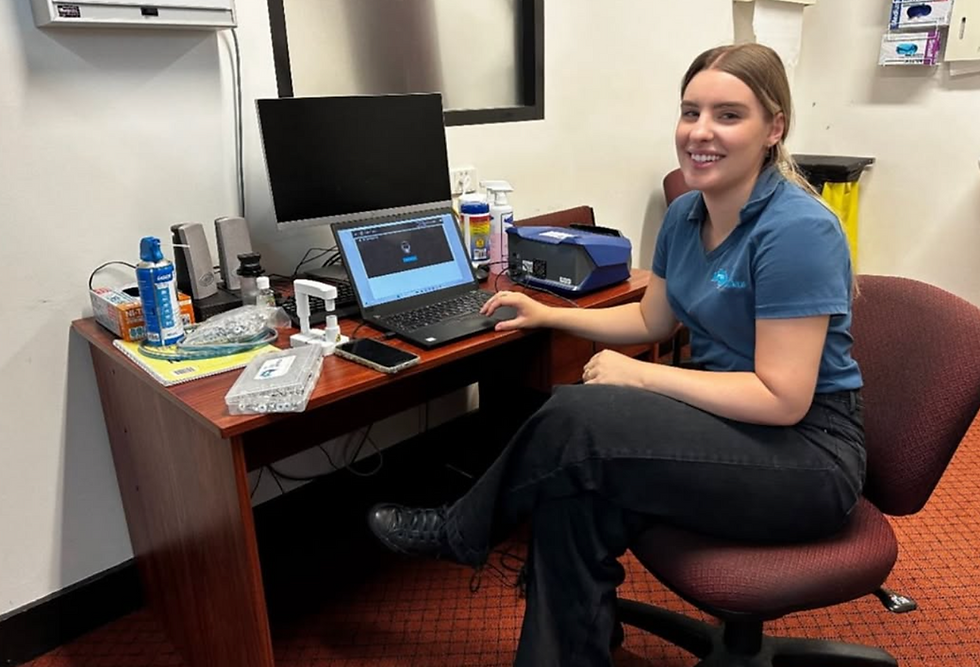
What Are the Australian & New Zealand Respiratory Protection Standards?
In Australia and New Zealand, respiratory protective equipment (RPE) must meet strict safety standards to ensure adequate protection against airborne hazards. The key standards governing respiratory protection include:
AS/NZS 1715:2009 – Selection, Use & Maintenance of Respiratory Protective Equipment (RPE)
This standard provides guidelines for choosing the right respiratory protection, ensuring proper use, and maintaining equipment to guarantee ongoing effectiveness.
AS/NZS 1716:2012 – Respiratory Protective Devices
This sets out the performance requirements for respirators and other respiratory protective devices, ensuring they meet safety and filtration standards for different workplace environments.
AS/NZS ISO 16975.3:2023 – Fit Testing for Respiratory Protective Devices (Newly Adopted Standard)
As part of the ongoing adoption of international ISO respiratory protection standards, Australia has now adopted ISO 16975.3:2007 as a local standard under the designation AS/NZS ISO 16975.3:2023. This standard provides specific guidelines for conducting fit testing of tight-fitting respiratory protective devices (RPDs), ensuring they form a proper seal and provide the intended level of protection.
Key aspects of AS/NZS ISO 16975.3:2023 include:
Fit testing methodologies, including QLFT-ATT (Qualitative Fit Testing - Aerosol Taste Test), QNFT-CNC (Quantitative Fit Testing - Condensation Nuclei Counter), and QNFT-CNP (Quantitative Fit Testing - Controlled Negative Pressure).
Competency requirements for fit test operators.
Fit testing procedures, interpretation of results, and proper record-keeping.
This standard aligns closely with RESP-FIT accreditation competencies, meaning there will be minimal changes for accredited fit testers. Additionally, many state and territory workplace safety regulators base their fit testing competence requirements on ISO 16975.3:2017, which is now fully incorporated into AS/NZS ISO 16975.3:2023.
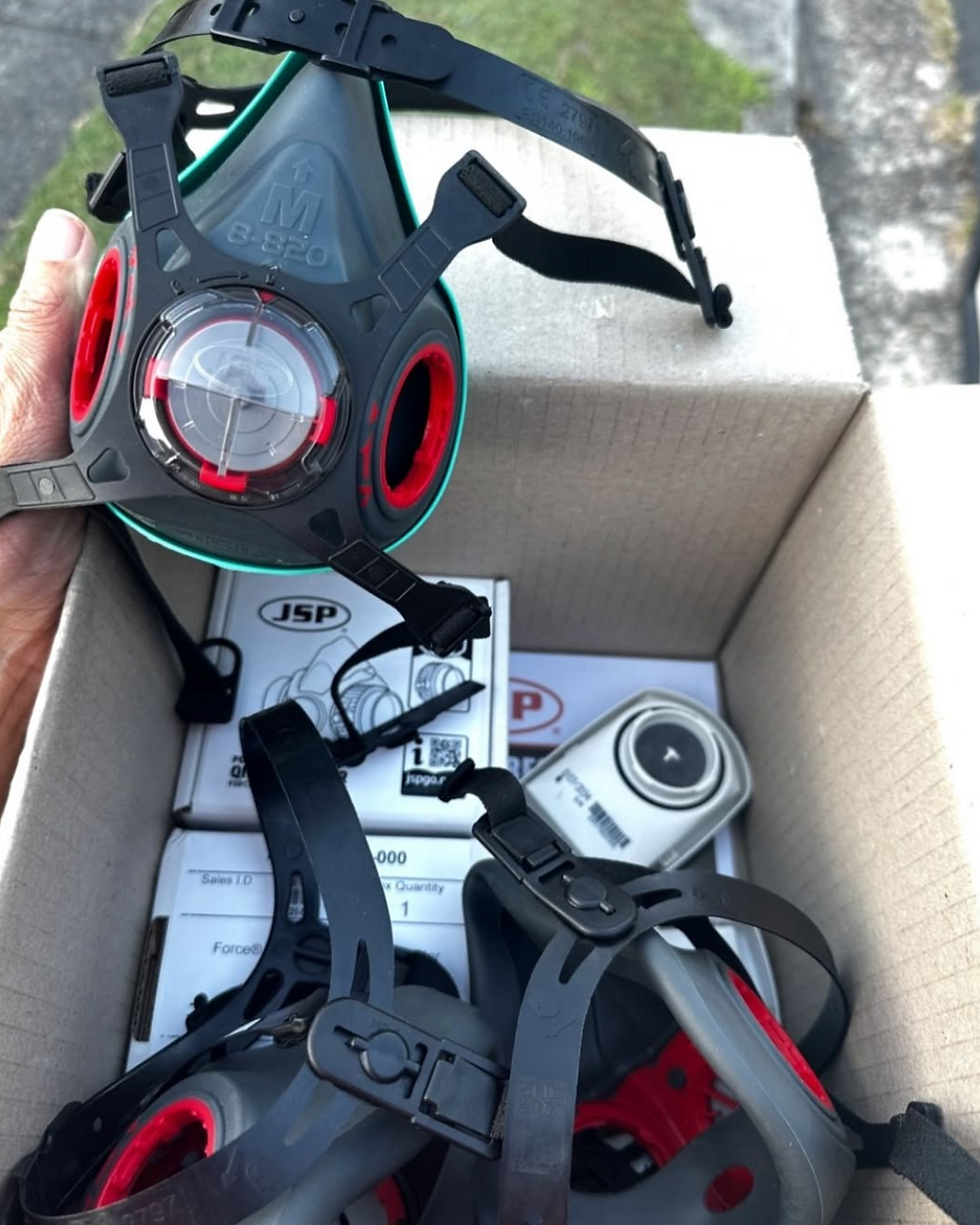
What’s Changing?
While the newly adopted AS/NZS ISO 16975.3:2023 is now part of the respiratory protection framework, AS/NZS 1715:2009 and AS/NZS 1716:2012 remain current. However, these older standards are set to be phased out by 2029, allowing a five-year transition period for businesses to align with the latest international standards.
What Do These Standards Mean for You?
The adoption of respiratory protection standards in Australia and New Zealand directly impacts workers, employers, and consumers. Whether you're on a job site, managing workplace safety, or purchasing respiratory protective equipment, understanding these regulations ensures you are making informed and compliant choices.
For Workers
Your safety depends on using certified respiratory protective devices (RPD) that effectively filter out hazardous substances. These standards help ensure that the masks, respirators, or breathing apparatuses you use have been tested for performance and reliability. Fit testing is also crucial—without a proper seal, even the best respirator won’t provide full protection. Make sure your employer provides correctly fitted equipment that meets AS/NZS 1716:2012 standards and undergoes annual testing.

For Employers & Businesses
Businesses have a legal responsibility to provide adequate respiratory protection for their employees. This means selecting RPD that comply with AS/NZS standards, ensuring workers are fit-tested, and maintaining equipment according to regulatory requirements. Compliance isn’t just about avoiding fines—it’s about preventing workplace illnesses and injuries. With recent updates, including the adoption of ISO 16975.3:2023 for fit testing, businesses must stay up to date with changing requirements and implement best practices for respiratory protection programs.
For Consumers
Not all masks and respirators on the market meet Australian and New Zealand safety standards. If you’re purchasing RPD for personal use, check for compliance markings, such as AS/NZS 1716:2012, to ensure the product has been tested for efficiency and fit. Be cautious of counterfeit or uncertified products, as they may not provide the level of protection required in high-risk environments. Fit Test Australia has extensive data that supports this concern.
By understanding these standards, everyone—from frontline workers to business owners and consumers—can make informed decisions that prioritise health and safety.
How to Ensure Compliance with AS/NZS Standards
Adhering to Australian and New Zealand respiratory protection standards is essential for workplace safety. Compliance not only protects workers from hazardous airborne contaminants but also ensures businesses meet legal obligations. Here’s how to ensure your respiratory protective equipment (RPE) meets AS/NZS standards.

1. Checking for Certification
Always check for compliance markings on masks, respirators, and breathing apparatus. Certified products should meet AS/NZS 1716:2012 for respiratory protective devices.
Look for markings such as "AS/NZS 1716:2012 Approved" or certification from accredited bodies to verify that the equipment meets required filtration and performance standards.
Avoid counterfeit or uncertified products, which may not provide adequate protection.
2. Proper Fit Testing
A respirator is only effective if it forms a proper seal against the face. AS/NZS ISO 16975.3:2023 specifies requirements for conducting fit testing.
Two primary fit testing methods include:
Qualitative Fit Testing (QLFT-ATT) – Uses a test agent (such as a bitter or sweet solution) to check for leaks.
Quantitative Fit Testing (QNFT-CNC, QNFT-CNP) – Uses specialised equipment to measure leakage around the mask.
Fit testing should be conducted regularly, especially when switching brands or models, or if facial changes (e.g., weight loss, surgery, facial hair growth) affect the seal, preferably by a RESP-FIt accredited fit testing company, so that you have the assurance that your fit test has been conducted properly.

3. Maintenance & Storage
Respiratory protective equipment must be properly maintained to remain effective. Follow manufacturer guidelines for:
Cleaning & Disinfection – Regularly clean reusable respirators with mild detergent and disinfectant.
Filter Replacement – Replace filters and cartridges according to usage frequency and contamination levels.
Proper Storage – Store RPE in clean, dry environments away from direct sunlight, contaminants, and extreme temperatures. Improper storage can degrade filters, compromise protection and can also deform the original seal of the facepiece, leading to excessive leakage.
4. Workplace Training
Employers must ensure that workers are trained in the correct use, fitting, and maintenance of their respiratory protection.
Training should cover:
How to correctly wear and adjust respirators.
How to conduct seal checks (fit checks) before each use.
When and how to replace filters and cartridges.
Recognising the signs of respirator failure or contamination.
Regular refresher training helps maintain compliance and ensures all staff remain aware of best practices.
By following these steps, businesses and workers can ensure compliance with AS/NZS standards, reduce the risk of respiratory hazards, and maintain a safer work environment.
The Risks of Non-Compliant Respiratory Protection
Using respiratory protective equipment (RPE) that does not comply with AS/NZS 1716:2012 standards can have serious health, legal, and financial consequences. Whether it's a worker unknowingly using a substandard mask or a business failing to meet regulatory requirements, non-compliance can lead to significant risks. Only a QNFT fit test will detect a counterfeit or sub standard RPE.
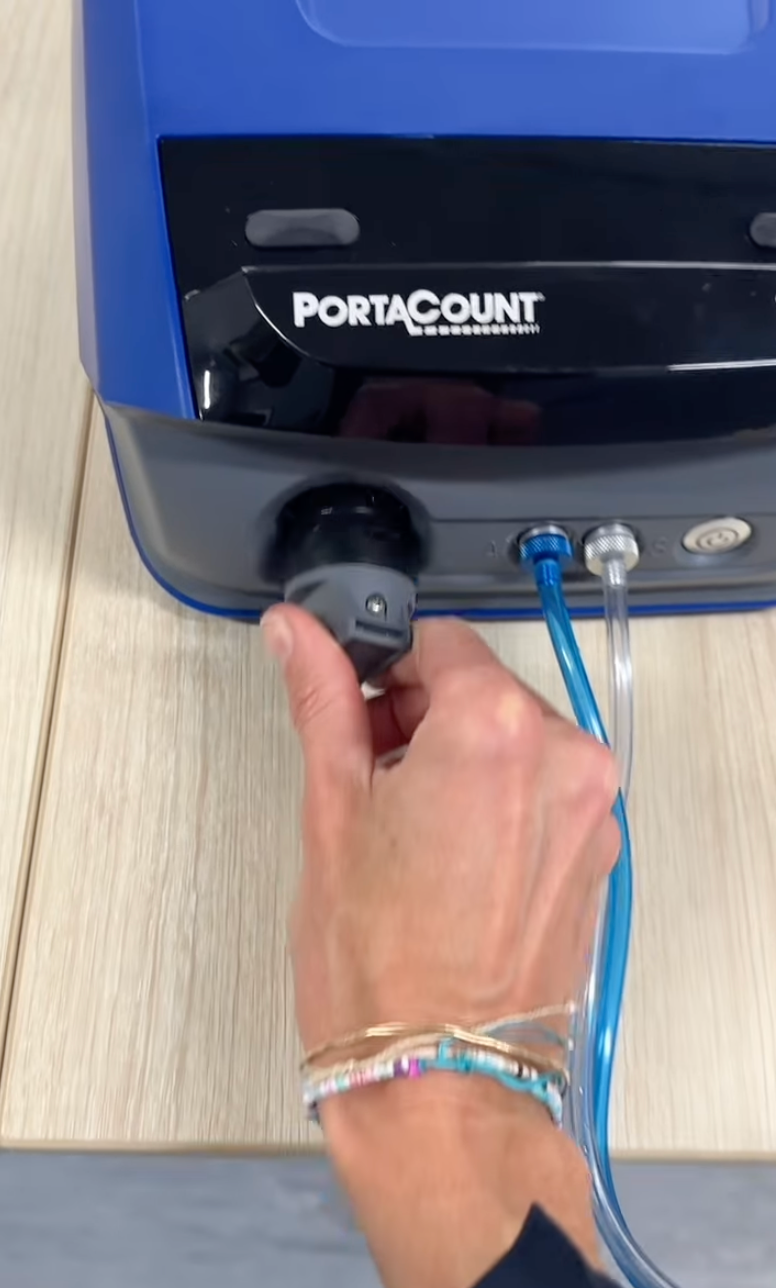
1. Reduced Protection & Health Hazards
Unapproved or counterfeit masks often fail to provide adequate filtration, exposing workers to hazardous airborne particles such as dust, fumes, and toxic vapours.
Poorly fitted or low-quality respirators may allow dangerous substances to bypass the filter, increasing the risk of lung diseases, respiratory infections, and long-term health complications.
In high-risk industries (e.g., mining, healthcare, construction), ineffective respiratory protection can lead to occupational diseases like silicosis, asbestosis, and chemical exposure-related conditions. Firefighters with inadequate respiratory protection will face smoke inhalation, which can be fatal.
2. Legal & Compliance Risks for Businesses
Employers are legally responsible for providing safe and compliant respiratory protection under workplace health and safety regulations.
Failure to comply with AS/NZS 1716:2012 and AS/NZS 1715:2009 can result in hefty fines, legal action, and potential workplace shutdowns.
If an employee suffers a work-related illness due to inadequate RPE, businesses may face compensation claims or penalties from workplace safety regulators.
3. Financial Consequences of Non-Compliance
Purchasing low-quality or non-compliant RPE can be a costly mistake, leading to frequent replacements of respirators, increased medical costs, and lost productivity due to worker illness.
Regulatory fines for non-compliance can run into thousands of dollars, damaging a company’s reputation and profitability.
Workplace incidents due to inadequate respiratory protection may increase insurance premiums and create long-term financial strain. Failing a fit test would also mean you need to purchase higher quality products/RPE, and reorganise another fit testing session, costing more money.
4. How to Avoid These Risks
Always source respiratory protective equipment from reputable suppliers and check for AS/NZS compliance markings.
Regularly conduct fit testing (AS/NZS ISO 16975.3:2023) and ensure workers receive proper training on RPE usage and maintenance.
Stay updated with changes in respiratory protection standards to ensure continued compliance and worker safety.
Investing in high-quality, compliant respiratory protection isn’t just about meeting regulations—it’s about safeguarding lives and ensuring a safer workplace for everyone.
Protect Yourself & Your Workplace: Stay Compliant with AS/NZS Standards
Ensuring compliance with AS/NZS respiratory protection standards isn’t just about following regulations—it’s about safeguarding health, reducing workplace risks, and maintaining a safe environment for everyone. Whether you’re a worker, employer, or consumer, taking proactive steps to use certified respiratory protective equipment (RPE) can make a significant difference in preventing harmful exposure to airborne hazards.
How to Stay Compliant

Purchase Certified Respiratory Protection – Always check for AS/NZS 1716:2012 certification when buying masks or respirators. This ensures they meet the necessary filtration and safety requirements.
Schedule Workplace Fit Testing & Compliance Checks – Employers should conduct regular fit testing (AS/NZS ISO 16975.3:2023) to ensure workers’ RPE provides the best possible protection.
Provide Training & Proper Maintenance – Ensure all staff know how to wear, store, and maintain their respiratory protection to maximise effectiveness and longevity.
Take Action Today
Don’t leave workplace safety to chance—protect yourself, your employees, and your business by ensuring all respiratory protection meets Australian & New Zealand standards.
🔹 Need to purchase certified respiratory protection? Browse a range of AS/NZS-approved masks and respirators (link to store)
🔹 Unsure if your workplace is compliant? Book a workplace compliance check to assess your current respiratory protection program and ensure you meet all regulatory requirements.
Your health and safety depend on the right protection—make the right choice today!
Relevant Legislation and Standards NSW
Category | Legislation/Standard | Description |
Workplace Health & Safety | Work Health and Safety Act 2011 | Provides a nationally consistent framework to secure the health and safety of workers and workplaces. Workers must take reasonable care for their own safety and ensure their actions do not endanger others. |
Workplace Regulations | Work Health and Safety Regulation 2017 | Division 5, Section 44 (3) outlines measures to prevent or minimise risks in the workplace, specifically addressing PPE suitability, fit, maintenance, hygiene, and use. |
AS/NZS 1715:2009 & Rule 1:2023 | Selection, use, and maintenance of respiratory protective equipment. | |
AS/NZS 1716:2012 | Sets performance requirements for respiratory protective devices. | |
AS/NZS 16975.3:2023 | Selection, use, and maintenance of respiratory protective devices – Part 3: Fit-testing procedures. | |
International Standards | AS/NZS 16975.3:2023 | Aligns with international best practices for respiratory protection fit-testing. |
OSHA 1910.134 | Occupational Safety and Health Standards – Respiratory Protection (USA). |
Comments